Cross flow filtration
in a few words
Membrane filtration is a purification process used to separate particles from soluble compounds in a liquid flow, based on their physical size, which is very often closely correlated to their molecular weight . With cross flow filtration (CFF), also called tangential flow filtration (TFF), the fluid flows tangentially to the filtration membrane and only a portion will flow across thanks to the pressure applied, instead of having all the flow frontally passing through, while particle would accumulate at the surface of the media.
It is therefore a pressure-driving purification technology, where the thinner the membrane porosity is, the more resistance you have to the permeation flow and more pressure (or power) you need to apply. The membrane filtration can be used for clarification (suspended particles or turbidity removal), concentration of one group of molecules (versus smaller ones) or soluble removal (thanks to diafiltration). At industrial scale, it can be designed in systems running in batch fed-batch or continuous mode.
Cross-flow filtration is widely used in various industries and with various types of membranes, including sugar, sweeteners, dairy, biomass fractionation and fermentation.
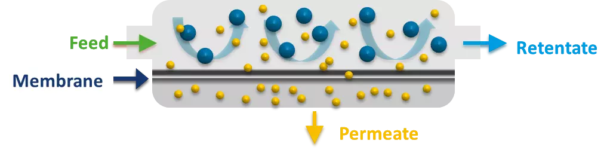
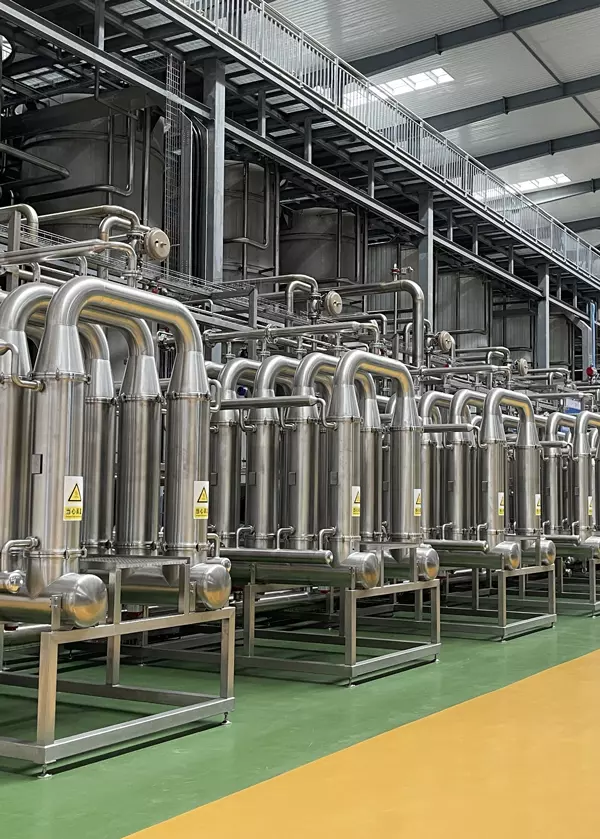
Membrane Filtration
A membranes systems
& winning combination
For more than 4 decades, we have been designing, building and commissioning optimized industrial solutions for microfiltration (MF), ultrafiltration (UF), nanofiltration (NF) and reverse osmosis (RO).
We offer a full range of state-of-the-art technologies for Cross Flow Filtration, also sometimes called Tangential Flow Filtration (TFF):
- Ceramic membranes, modules and units for MF and UF.
- Organic membranes, modules and units for UF, NF and RO.
- Full set of ancillary pieces of equipment, among them Cleaning in Place units, which guarantee steady and long lasting membranes performances.
Our processes development services can then design virtually any kind of challenging process, especially yours.
Ceramic membranes,
modules and units for MF and UF
Membranes
Our Kerasep™ ceramic membranes offer many advantages for industrial processes:
- Superior performance in a more compact design (ratio of surface versus volume has been maximized).
- Ultra-resistant to high temperatures and extreme pH for extra long durability.
- Kerasep™ membranes are also highly resistant to back-pulse cycles.
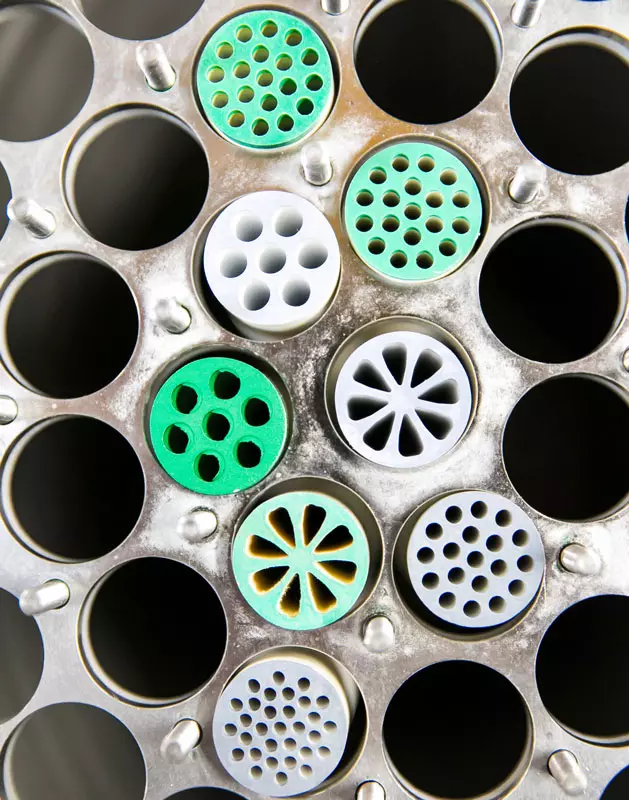
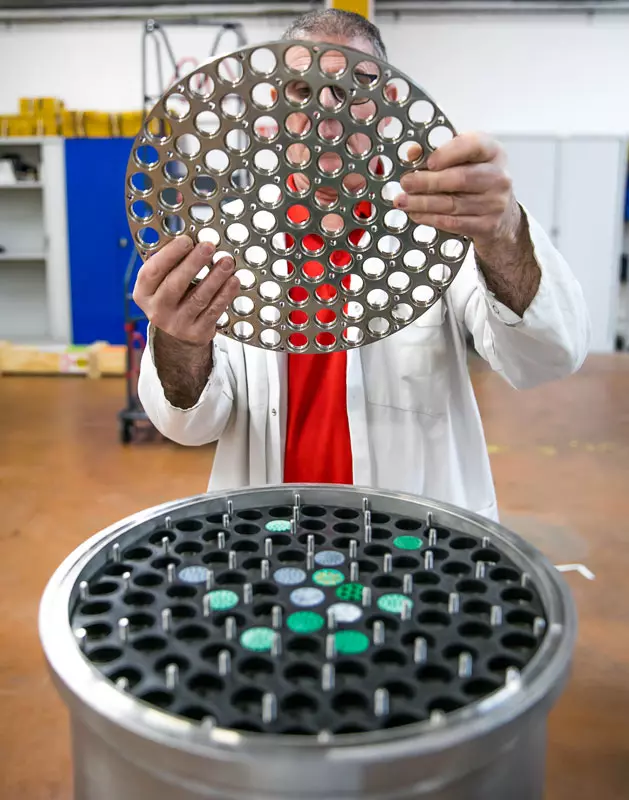
Modules
Improve the benefits of your membranes with Applexion’s Kerasep™ modules:
- Accommodates from 1 to 138 membranes.
- High quality welding for longer durability and robustness.
- A clever sealing technology with our proven Kerasep™ single-piece gasket: 15 years of use under industrial conditions, usable for many products and applications.
- A more compact design to allow the flexibility to fit more membranes in the same space.
- User-friendly and easy to maintain.
Kerasep™ modules have been recognized by the industry for their quality and robustness for decades. Their optimized design ensures high cleanability and excellent performance in operations.
Thanks to our smart single-piece gasket technology, Kerasep™ modules are easy to inspect and maintain.
Systems
With a strong and recognized experience in membrane design, CFF process development, and industrial plant engineering, construction and commissioning, Applexion teams are able to provide you with complete and optimized CFF units.
Thanks to process modelling, data computerization and engineering expertise, we design CFF units combining high-performance, efficient process integration and balanced CAPEX/OPEX. With our pilot units, and by performing in-depth feasibility studies focused on your objectives, we are able to deliver industrial solutions with guaranteed process performance.
Applexion’s Jumbo Skid is an innovative unit composed of 2 times more modules for the same footprint on the ground. This outstanding design brings interesting benefits for your process line:
- Largest filtration working area.
- Optimized layout for a reduced footprint and CAPEX.
- Lower power consumption rate per filtration surface.
Jumbo Skid exits in two sizes:
- 16 modules for an 8-module footprint.
- 20 modules for a 10-module footprint.
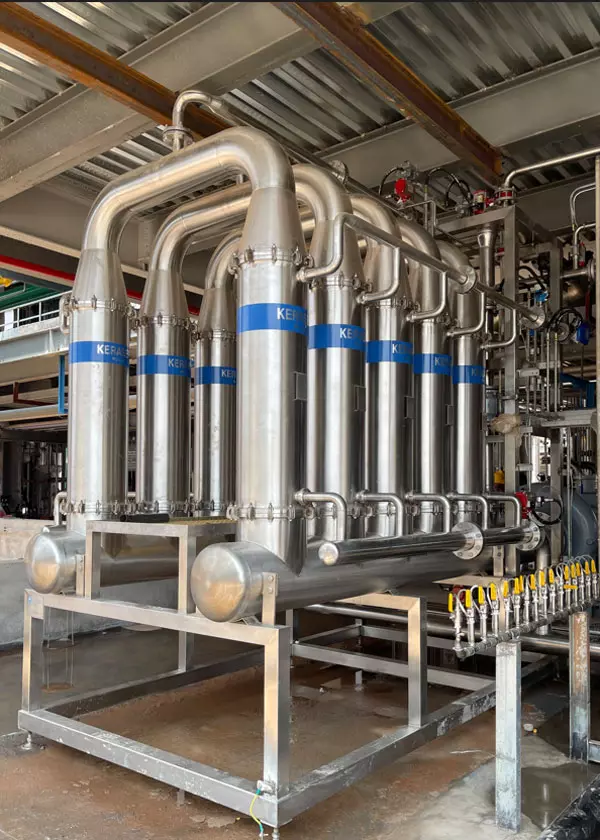
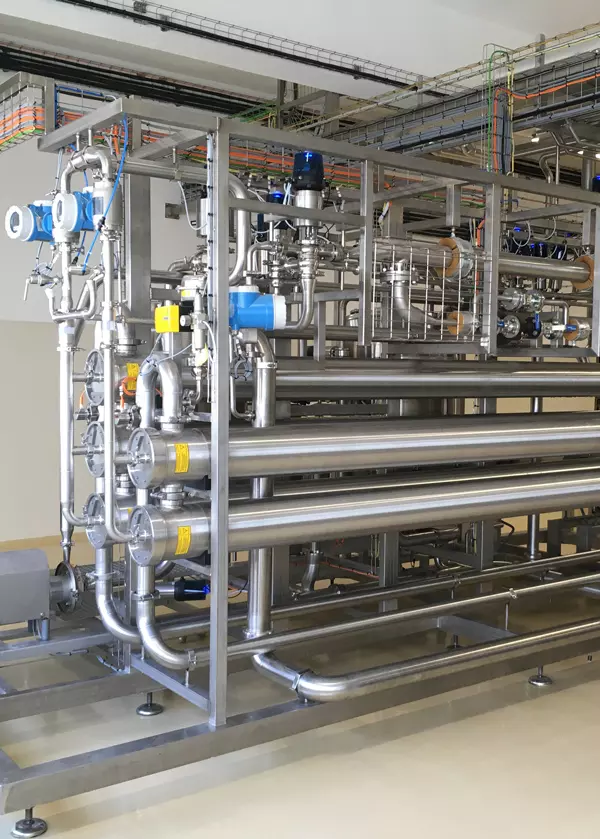
Organic membranes,
modules and units for UF, NF and RO
Membranes
Organic membranes are polymer based and are the technology of choice for nanofiltration and reverse osmosis.
The Applexion™ NF 150 and NF 300 membranes are cost-effective organic spiral nanofiltration membranes, highly resistant and specifically well-adapted for industrial processes.
In addition to a large filtration area, you will benefit from:
- High resistance allowing you to use the membrane under harsh conditions including broad range of pH (2-14), high temperatures (5-80°C) and operating pressures (5-20 bar).
- Excellent retention of high molecular compounds (oligomers, colorants, divalent ions, etc.).
- High permeate flow rates from 5 – 10 m3/h.
- Low energy consumption.
- Easy to set up and to maintain: membrane replacement is quick and easy by employing our user-friendly membrane extractor.
Modules & Systems
The tube housing is designed to receive 2 to 5 membranes per tube housing. Also designed to resist extreme pH, pressure, and temperature, it is compliant with the ASME pressure vessels code.
In addition, we can supply accessories such as:
- Tube housing accessories including end-plates, spacers and inter-connectors.
- Membrane extractors to extract the membrane easily and safely.
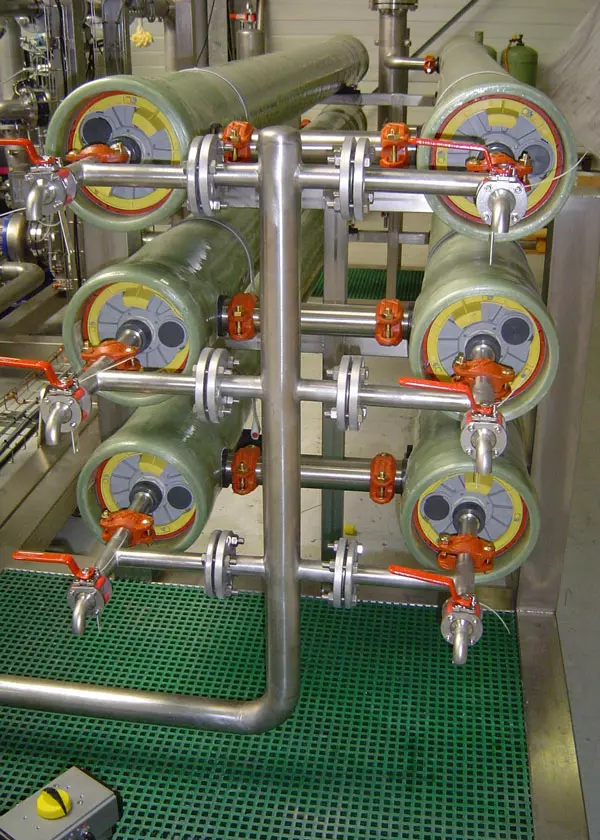
Membrane filtration
Filtration system design
we minimize scale up risks, we shorten time to market and we maximize performance and cost efficiency.
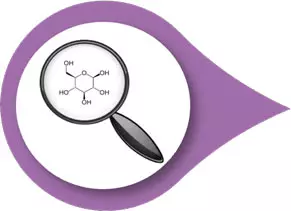
The very first point to start is the definition of the raw material to be purified. Which enables to define the final quality of the product and types of impurities to be removed. The quantity and the nature of these impurities will determine what pretreatments are recommended and which strategy of purification to be implemented (batch or continuous, carrousel mode, diafiltration,…).
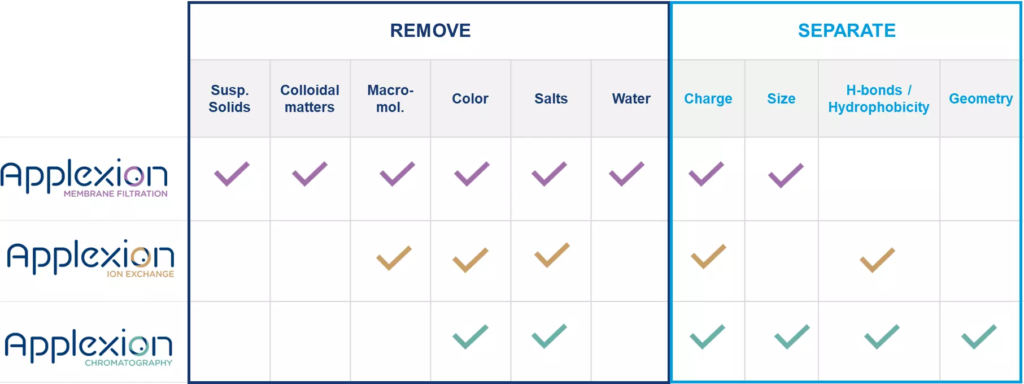
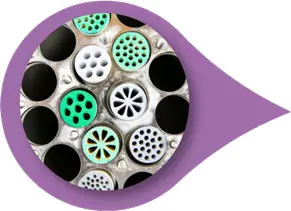
A screening of different membranes is systematically performed at lab scale. Priority is to define best cut off (according to final product specifications), then to select most appropriate geometry. The goal is to explore and collect data to properly compare the different geometries and cut off in terms of quality, yield, cross flow velocity, cleaning, eventually backpulse efficiency.
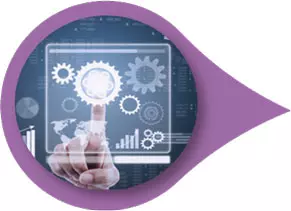
One of the unique expertise of Applexion for a process development is digital modeling and process simulation. By combining experimental results of the current project, previous experience and our unique in-house software, we considerably increase the reliability of our results and hence the confidence in estimations that we can deliver at early stage of process development.
Numerical approach requires less raw material, smaller size of equipment and less time to explore a wider range of solutions. Moreover, it gives the capacity to test a broader range of constraints, without adding time for extra piloting, and to investigate in details the robustness of the design of the process. It is key for all new applications, where decades of feedbacks and learning are not available. Especially when time to market is key to succeed in launching innovative ingredient or food product.
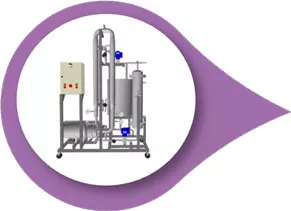
The piloting step is implemented to explore and push performances of the selected membrane to their limit in order to collect data for industrial design and optimization. Considering membrane selection and piloting work, many of Applexion customers do prefer to conduct experiments by themselves for convenience (product integrity, transport and travel constraints) and to keep hands-on the product. They enjoy the availability of our membranes and pilot units, and Applexion support:
- remotely by our expert or a dedicated engineer
- local assistance and training
- tutorials and templates to organize and well document trials for a robust scale-up
- scale-up and process design based on your data.
Pilot trials are a key step for the successful development of your industrial unit.
This series of 8 video tutorials is aimed at helping to organize trials for a robust scale-up.
Contact us to fine tune trials organization and scale-up
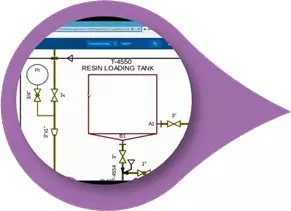
The precise process design given with process performance guaranteed is the natural outcome of all these previous steps. At each step, an open dialogue with our customers allows for a final design customized to your specific needs and compliant with Applexion quality standards.
Membrane filtration
Applications
Membrane filtration is a versatile technology that can be applied with adapted quality grades to most industrial applications:
- Bulk fermentation (antibiotics, food additives, ferments, enzymes, organic acids, …).
- Whey, milk and dairy derivative products (such as proteins concentrates and isolates).
- Sugars, sweeteners, polyols and derivatives.
- Beverages (beer, wine, water, fruit juice, etc..).
- Highly demanding pharmaceutical and biopharmaceutical applications (API, IGs, vaccines, …).
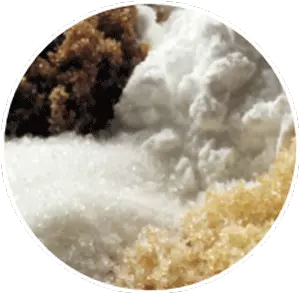
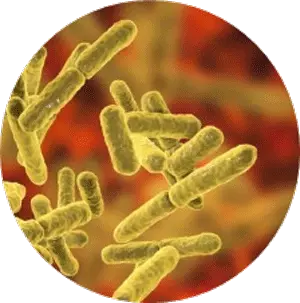
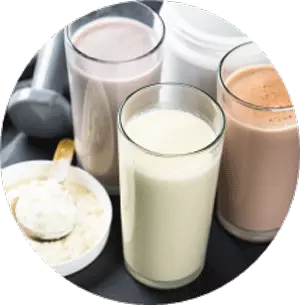
Frequently Asked Questions
What are the main costs of using membrane filtration technologies?
- Electric power, needed to circulate the product towards the membrane surface and provide the necessary pressure for filtration. The membrane geometry, membrane surface, general arrangement of the system and ways it is operating, by design and in daily operation, are key to optimize power consumption. You can easily find a factor of 2 to 5 between two ways for a same job to do! Pilot trials is the first place and time for such investigation. Daily optimization, with smart controls and support of digital services are of great help for the largest systems.
- Cleaning in place: Water, heat, cleaning agents can be drastically optimized, through optimization of CIP frequency, cleaning only the necessary sections when performance drops require it, and ways the cleaning is done. Similarly, a versatile design and control combined withe support of digital services are key for daily optimization of the performance.
- Membrane replacement: Ceramic membrane a great for heavy duty separation. Their chemical and temperature resistance basically makes them last forever in a smooth mechanical and hydraulic environment. In industrial conditions, quality of the pre-treatment and mechanical resistance of the membrane, still maintaining high flux and great compacity, makes the difference. Our Kerasep diamond 2 membrane is the reference, and our +50 years’ experience in very various industrial environments make the difference.
How to choose membrane filtration technology among alternative technologies?
That is a long story and hard to make it short! Depending on the cut off, from Microfiltration to Reverse Osmosis application, the technology benchmark will be different. Few examples however:
- in biotechnology, the targeted product needs to be separated from the biomass (or fermentation broth) . Laboratory bench technics generally are not scalable to industrial use, and one needs to determine the right moment to work on the up-scale. We know how critical the fermentation step is to have a project flying. Experience shows that DSP (down stream purification) is key for project viability, and membrane filtration is generally the first step, often followed by other Applexion technologies. Do not hesitate to contact our specialist, it is never too early!
- for product / salt separation, nanofiltration often comes into play. And the main technology alternative is industrial chromatography. Both being Applexion technologies, we would be pleased to customize the benchmark for your application, contact us.
- for concentration. Reverse Osmosis technology allows for water separation from basically any other component of the product you wish to concentrate, and therefore is an alternative to evaporation. Not requiring any change of state from liquid to vapor, it is much less energy intensive than evaporation, with related savings in carbon emission.
Can I modify my existing filtration unit?
Yes, in most cases, existing filtration units can be modernized to ensure lower power consumption, lower CIP costs and higher membrane lifetime. We do bring special care to water savings, thanks to smart water recycling and reuse. Applexion has developed specified “performance boosters” addressing specifically these topics and their integration can be further studied through our “Upgrade and Revamp” offers.
Why choose Applexion?
and offering on Chromatography, Ion exchange and Membrane filtration technologies.